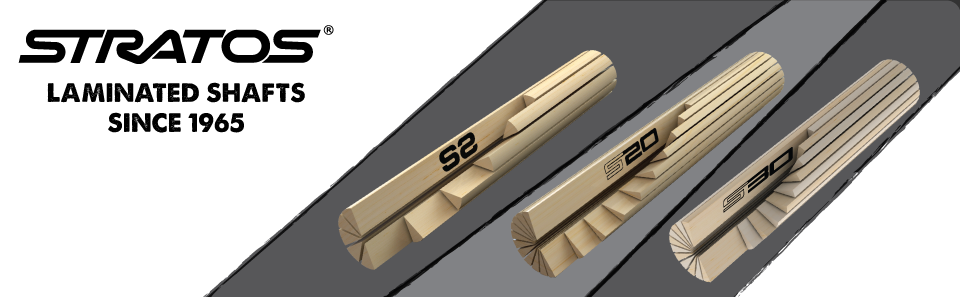
![]() |
THE CONCEPT OF STRATOS
Wood classic shafts are heavily anisotropic and release uncontrollable forces during hit.
Renzo Longoni in the late sixties deeply analyzed the problem coming to the conclusion that nature has to be recreated. He decided to cut slices of wood, select them by weight, straight venner and quality to recreate a perfect shafts using just best pieces. Laminated shaft was born and patented in 1985. |
![]() |
JBR2 FERRULE, G10 CORE AND LD TECHNOLOGY
Improving constantly the quality of the game is one of the primary goal of the Longoni team.
To guarantee the maximum gaming performance of the Longoni shafts, we worked a lot on their frontal part introducing the new JBR2 ferrules by Longoni with high density G10 support and a proprietary system to reduce deflection, improving acoustics. |
![]() |
VIBES-FOAM
In order to improve the balance and acoustic, in all laminated shafts close to the joint area, we created a long hole filled with a special foam. This material compensates density, absorbs vibrations and improves the balance.
|
![]() |
THE RIGHT PLACE FOR THE RIGHT WOOD
This point is crucial: Stradivari was used to go and choose the best wood in the valley of Panaveggio, where the fir trees grew in a unique microclimate in the world.
Longoni company uses for its shafts only the best hard rock maple from Quebec (Canda) and the whitest european hornbeam, where extreme low temperatures, sun light and ground provide the best quality of wood for the billiard game. |
![]() |
CUTTING PROCESS The cutting of the logs is done during the coldest periods of the year to get the best physical features and that white color which distinguishes the best shafts: the Longoni shafts. From the central parts of the boards are extracted the elements that must have straight and thick vains without the presence of knots or other ahestetic blemishes including the sugar strips which can cause spots typical of the Saccharum maple. |
![]() |
DRYING PROCESS The drying process already begins when you cut the log into boards and leave them at open air, in the extreme dry and freezing climate where they are grown. Once the elements are obtained from the boards, these are vacuum dried to mechanically remove most of the water hold by the cells. After the first turning, all the Longoni shafts are left in a special climate-controlled and constant drying room for at least one year in order to loose totally the last traces of moisture before proceeding to the stabilizing process. |
![]() |
STABILIZING PROCESS The stabilizing of the wood is the process through which, from a completely dried material, the wood starts to absorbe the natural environmental humidity to reach the right balance with the outside world. Thanks to this process which takes at least 3 months after the drying room process, the shafts will remain stable over the time and they will ensure an excellent playability. |
![]() |
CREATING A LAMINATED SHAFT To create a laminated shaft, after having correctly dried and stabilized the raw material, the wood must be cut into slices, which have to be selected and glued with a combination of slow-hardening glues. The gluing of the laminated shafts takes a long time: for the right result it is necessary to leave the glued slices in special moulds for a minimum of 24 hours. This technique limits a lot the production capacity but it greatly increases the quality of the shaft. |
![]() |
S2, S20, S30... WHICH IS THE DIFFERENCE?
S2 has 10 highly selected Canadian hard rock maple slices. An elastic shaft with determination, perfect for the most extreme english. S20 is the first in the world to have a structure of 20 slices of Quebec hard rock maple which makes the shaft really innovative. The game is easy and natural and the deflection is completely erased.
Thanks to its internal structure the weight is well balanced.
S30 is the last Stratos: 10 slices of hard canadian maple combinated with 10 slices of balcan hornbeam. Made for the player likes strong, stable and with higher density.
|
![]() |
STRATOS LONGONI WARRANTY All Stratos shafts are univocally numbered to trace production date. Each shaft is also labelled to report product specification including code, name, diameter and exact weight .The label, beyond showing these data, is a further guarantee of authenticity. Before labelling, each shaft is individually checked on a test desk to avoid warpage and other defects. To help reporting correct weight and diameter, we use a precision digital scale connected to the system and a laser micrometer. |
![]() |
MADE WITH THE WORLD CHAMPIONS
Players of the Longoni team have an important role in the development of our shafts because it’s thanks to the skills of the best talents all over the world that we can create excellent shafts. All our models have been tested and approved by our champions in order to ensure the maximum results and satisfaction to our customers. The results speak for themselves: with our shafts the most important worldclass titles have been taken. |
![]() |
MADE IN ITALY: YESTERDAY, TODAY AND TOMORROW
All Longoni shafts, including the laminated ones, are entirely and uniquely produced in Italy in the factory based in Mariano Comense with techniques and machineries developed by us. The processing cycle of each shaft lasts at least 24 months: from when you cut the board to when it reaches the billiard tables around the world. The choice to continue completely producing in Italy was dictated by the desire to have a product different from all the other ones in terms of quality and technology, always under a strict control of our staff. |
![]() |
STRATOS SHAFT: PRECISION AND TRACEABILITY
All Stratos shafts are univocally numbered to trace production date. Each shaft is also labelled to report product specification including code, name, diameter and exact weight .The label, beyond showing these data, is a further guarantee of authenticity. Before labelling, each shaft is individually checked on a test desk to avoid warpage and other defects. To help reporting correct weight and diameter, we use a precision digital scale connected to the system and a laser micrometer.
|
IMPORTANT NOTICE:
The company reserves the right to apply modifications or changes to the product without any obligation of previous notice.
The company reserves the right to apply modifications or changes to the product without any obligation of previous notice.